Intelligent scheduling thanks to telematics solutions
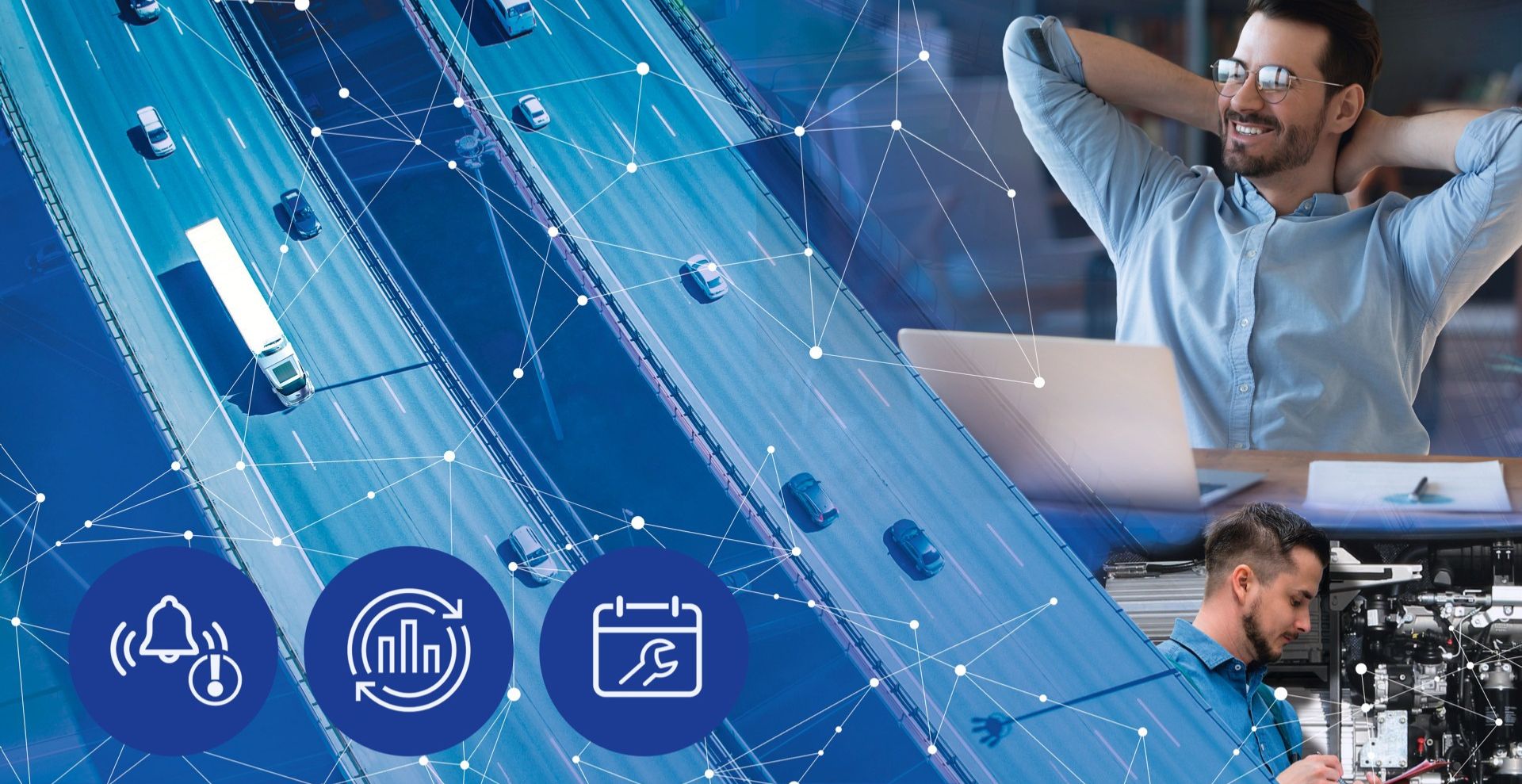
Waiting is no one’s idea of productivity. The wheels need to be turning for the company to earn money from its truck. So, it’s a good job that the freight forwarder in question has kept up with the times. The dispatcher knows all the traffic jam hot spots. And a quick glimpse at the telematics system is all it takes to spot the 14-kilometre traffic jam at the motorway junction. Thanks to real-time data, the freight forwarder knows the delivery is likely to be delayed until around 12:27 p.m. That’s the new estimated time of arrival and right in the middle of the machine manufacturer’s lunch break. So, what’s the plan now? Time to rearrange the delivery schedule. The dispatcher quickly logs into the recipient’s time window management system and books a new slot for 4pm. And the time until then won’t be wasted waiting around. Instead, it will be put to good use. The dispatcher uses a messaging service to instruct the driver to prioritise another unloading point that was originally scheduled after the machine manufacturer. The driver confirms the amended route.
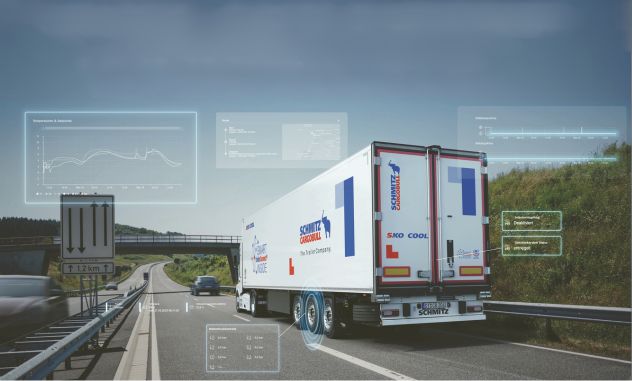
Rescheduling made easy
Thanks to modern IT systems, spontaneous rescheduling is no longer a major hassle. Freight forwarders have all the information they need, available to them in real time – and that’s all thanks to the advances made in the digitalisation of fleet management. With a single glance, they can see where their vehicles are located and what they’ve got on board. And a whole host of other data is relevant for their colleagues from fleet management. They can use dashboards to monitor details like brake wear, tyre pressure, or the next scheduled inspection. These dashboards allow them to use data retrieved from the FM interface in the vehicle. Fleet managers also benefit from remote access to evaluate data from the digital tachographs or driver maps, therefore enabling them to meet their legal requirements. This feature is known as tacho remote download.
Fleet managers also receive alarms when things are going pear-shaped – if it looks like the trailer or cooling unit is about to break down, for instance. This feature is known as proactive monitoring. Data can be analysed in the TrailerConnect® portal. The system detects any problems at an early stage, which means the dispatcher is informed quickly and can issue concrete recommendations for action. Service appointments can be planned proactively, and unexpected downtimes are avoided.
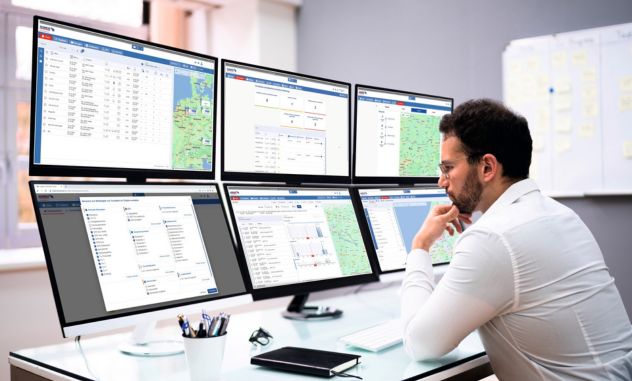
It is pretty hard to imagine that, in the past, dispatchers only had a phone, pen, and notepad to work with. And it is even harder to imagine there are obviously still some fleets that are foregoing these modern amenities and digital assistants in their day-to-day work, failing to utilise support from telematics systems or transport management systems (TMS). Even small fleets or companies that always cover the same routes can benefit from the use of IT solutions.
While the tractor unit was the focus and linchpin for telematics solutions for a long time, the towed unit is now increasingly coming into the spotlight. They often carry assets that are worth millions to the customer. And, in many cases, trailers or containers are not fixed to the tractor unit. That’s why it is important that the towed unit can be located separately to the tractor unit. In combined transport, for instance, the trailer is constantly changing its tractor unit. In traileryard concepts, the trailer is like a mobile warehouse that spends most of the time uncoupled in the yard. For this reason, modern scheduling and fleet management are focused around both the tractor and the trailer. In light of this, Schmitz Cargobull equips all of its new vehicles with TrailerConnect® telematics as standard. Via the TrailerConnect® portal or the beUpToDate app, dispatchers and fleet managers have access to all relevant data at any time. These applications can be used to plan and track routes and also intervene whenever necessary.
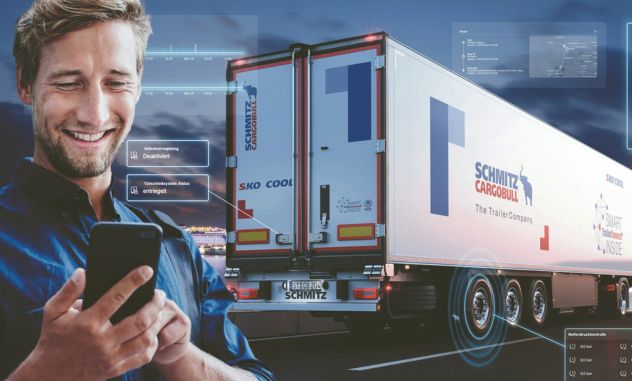
Intervention in the event of any deviations
Information on the trailer’s inner workings is exceptionally important, particularly for the temperature-controlled transportation of pharmaceuticals or food. The cooling unit is not a black box but completely transparent, delivering up-to-date temperature data on a continuous basis. In the event of deviations from the specified values, the dispatcher can intervene at any time. After all, every deviation presents a risk of industry standards or legal requirements being violated or of freight going bad or becoming unusable. And if that wasn’t bad enough, there is also the risk of annoying the customeAs essential as information from the trailer, swap trailer or container is, this is not the only data that is relevant for dispatchers and fleet managers. They use other systems to track information about the vehicle, its load and its planned routes. They look at the orders coming into the TMS, look for interesting freight or load capacity requirements in freight exchange platforms, and communicate with their forwarding agents or cooperation networks on a range of other portals. Because interface standards have now established themselves, the various applications can be combined to good effect these days. After all, if you are running various stand-alone solutions in parallel, you are missing out on synergies and shouldering inefficiencies, and you also run the risk of errors caused by multiple parallel data records. For this reason, an increasing number of IT providers offer solutions that integrate different applications. In the ideal scenario, the dispatcher will be using a central IT platform to keep an eye on all of their connected portals. Instead of monitoring lots of individual applications, they can orchestrate everything from one place. The Schmitz Cargobull TrailerConnect® system can achieve all of this as a central platform for efficient fleet management. No matter who the vehicles are manufactured by, all data from the fleet can be displayed on one platform. This facilitates efficient data management, streamlines workflows, and maximises trailer fleet availability and utilisation.
Sharing data, boosting benefits
If lots of data flows together on a single platform, this not only generates huge synergies for the individual company, but also for a number of other stakeholders with access to this data. Of course, settings have to be configured in advance to define which company has access to which data and with which authorisation level in order to protect the data and prevent its misuse. Breaking up data silos not only sheds light on the routes in your own fleet, but also reveals the movements and orders of other members in a cooperation network, for example. With the TrailerConnect® Data Management Center, various systems can be integrated centrally. Lots of different telematics systems and data are consolidated on one platform. Data is shared securely on an individual basis – for maximum control and transparency. With the additional TrailerConnect® TourTrack feature, journeys are tracked and transport data is shared on an order-by-order basis. The targeted and selective sharing of data for each route, route-based real-time monitoring including estimated time of arrival, and the automatic creation of order-based temperature reports create genuine transparency throughout the supply chain.
Data sharing can also be the ideal starting point for the use of AI within fleet management. AI can analyse vehicle deployment, routes, loading stops, and load searches, and then use this knowledge to make effective matching proposals. For instance, if a freight forwarder goes to the same unloading points three times a week – like the traffic-jam-plagued driver at the beginning – AI knows that a trailer will be free there on a regular basis. It can use a host of data to provide the dispatcher with bespoke proposals for suitable return loads.
Anyone who has already recognised the benefits of digitalisation is increasing their chances in the highly competitive transport market. Companies become more efficient, quicker and more transparent, and will be perceived completely differently by their customers. A freight forwarder that works with modern IT tools is always in a position to provide information about the status of a delivery or report potential damage immediately. The driver can use their tablet or smartphone with the telematics application to take photos of potentially damaged packages. By obtaining a digital signature from the recipient, they can create a delivery receipt straight after successful unloading. The customer does not need to actively request this data anymore and can even access it themselves at any time – provided they are connected to the system and hold the relevant authorisations. There are also benefits for the driver. There is less pressure on the driver because dispatchers can assign suitable routes that are in line with driving time recommendations with the support of AI. They can also train drivers on how to drive economically, while fleet managers can use telematics to detect anomalies in terms of wear or consumption.
Freight forwarders enjoy many benefits
Business owners also enjoy a range of different benefits when using telematics solutions: the capacity of load units is exploited as effectively as possible, significantly reducing empty trips. Fewer trips mean less consumption and lower carbon emissions. The risk of downtime is reduced as low tyre pressure, hot brakes or an impending cooling unit breakdown triggers an alarm straight away. Before the vehicle breaks down and has to be towed away for a high cost, the fleet manager can direct the vehicle to the nearest workshop, which of course is recommended straight away by the system and displayed along with its opening hours.
However, even the best telematics system has only a limited impact when it comes to dissolving traffic jams or affecting what is happening on the road. The integrated navigation system, which has been optimised to the needs of truck users, can recommend diversions for the driver. However, it is often too late to turn off the motorway or perhaps all the other road users have received the same recommendation to exit the main road. In this case, it is better to sit tight and wait for new instructions from the dispatcher.